The IAA Mobility 2023 will once again be held in Munich this year. In addition to the classic product and brand presentation on the trade fair grounds as part of the “Summit”, there will be a wide-ranging program in downtown Munich under the motto “Open Space” as well as the “Blue Lane”, a test track for sustainable mobility.
The KAMO: High Performance Center will also be represented at this year’s “Summit” at the joint booth of the Fraunhofer-Gesellschaft.
You will find our joint booth in hall B1 / booth D11.
We are looking forward to your visit!
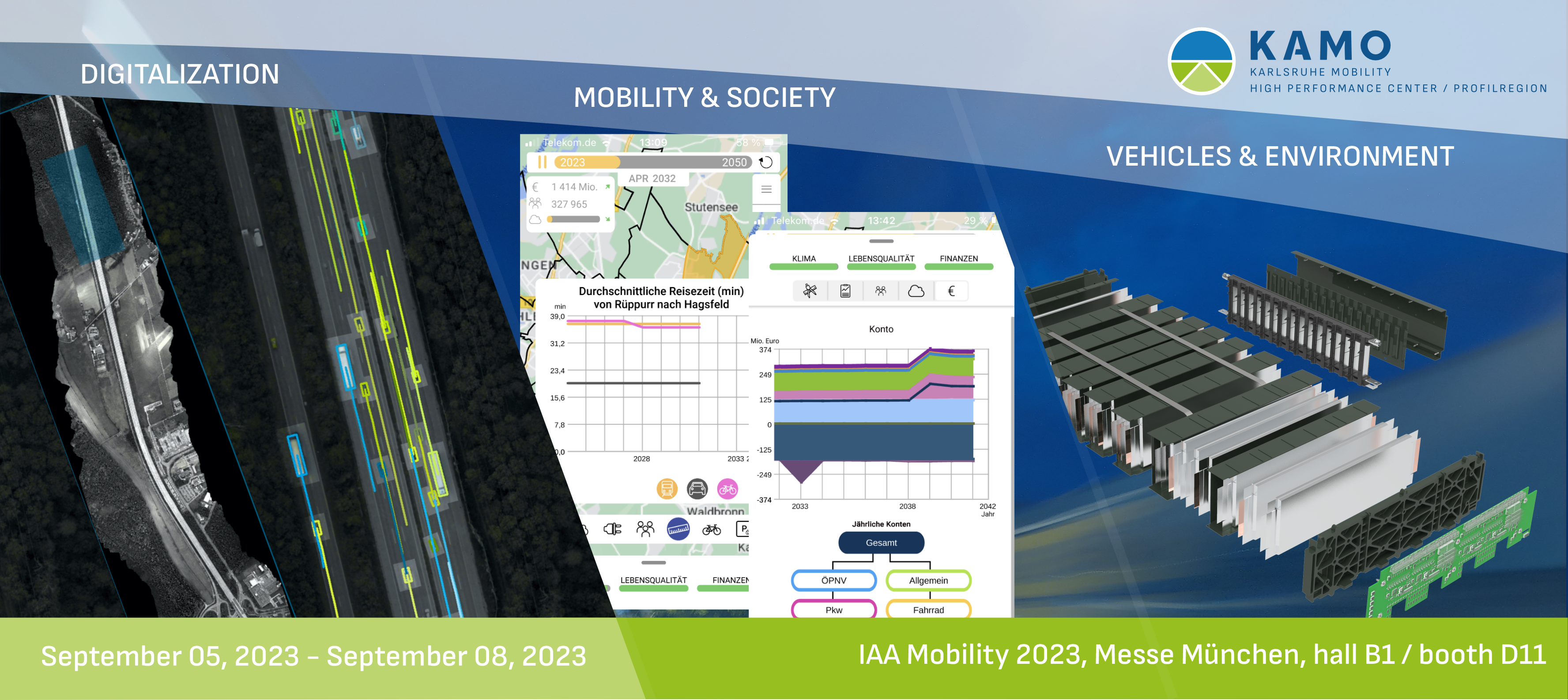
Personal preferences, social relationships
and available options determine our mobility
behavior
The mobility transition requires an intelligent networking of all mobility options. Besides achieving better individual mobility with less traffic, it is critical to reduce the environmental impact of vehicles and mobility systems. Digitization and AI can play a decisive role in development, testing, validation and system networking. In KAMO (short for »Karlsruhe Mobility«), we address current and future challenges faced by individuals, companies, local authorities and the environment through knowledge transfer, practical examples and smart technologies.
Mobility needs to change – but how?
How do you achieve climate neutrality as fast as possible, but without reducing quality of life or bankrupting local authorities? For a playful take on the changes to urban mobility up to 2050, Fraunhofer, KIT and Takomat GmbH have developed the app MobileCityGame, with the support of the Federal Ministry for Education and Research (BMBF). »The MobileCityGame allows players to experiment on their own smartphones to come up with ecologically and financially sustainable mobility systems,« says project leader Dr. Claus Doll from the Fraunhofer Institute for Systems and Innovation Research ISI and KAMO research leader for mobility and society. Currently, the app maps Karlsruhe with its 300,000 inhabitants, 27 city districts and 15 surrounding districts. All passenger transport options including e-vehicles and car sharing are considered. Players in the app can try to make transport systems climate-neutral, convenient and financially viable.
The intuitive user interface enables future scenarios to be developed within 20 to 30 minutes. »For example, you can build cycle lanes, set up charging stations for electric vehicles or tweak parking fees,« says Dr. Susanne Bieker, who is also a project manager at Fraunhofer ISI. »As you play, you need to consider the impact of each decision on the climate, quality of life and the municipal budget.«
The MobileCityGame was developed as a tool for sustainable urban planning as well as for research, teaching and social dialogue. A beta version for testing is currently available to anyone who is interested. The official release in the Apple App Store and Google Play Store is scheduled for the end of August 2023. For more information and updates on current download opportunities, visit www.isi.fraunhofer.de/mcg.
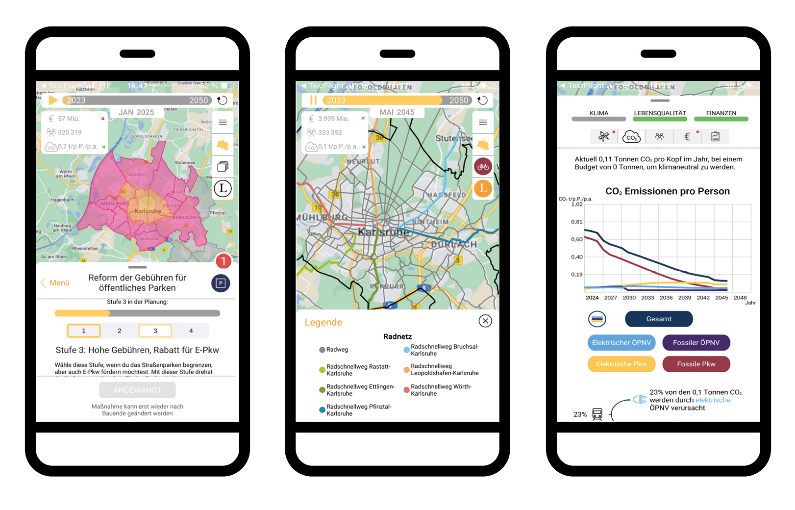
How do we ensure that highly automated and autonomous driving is safe?
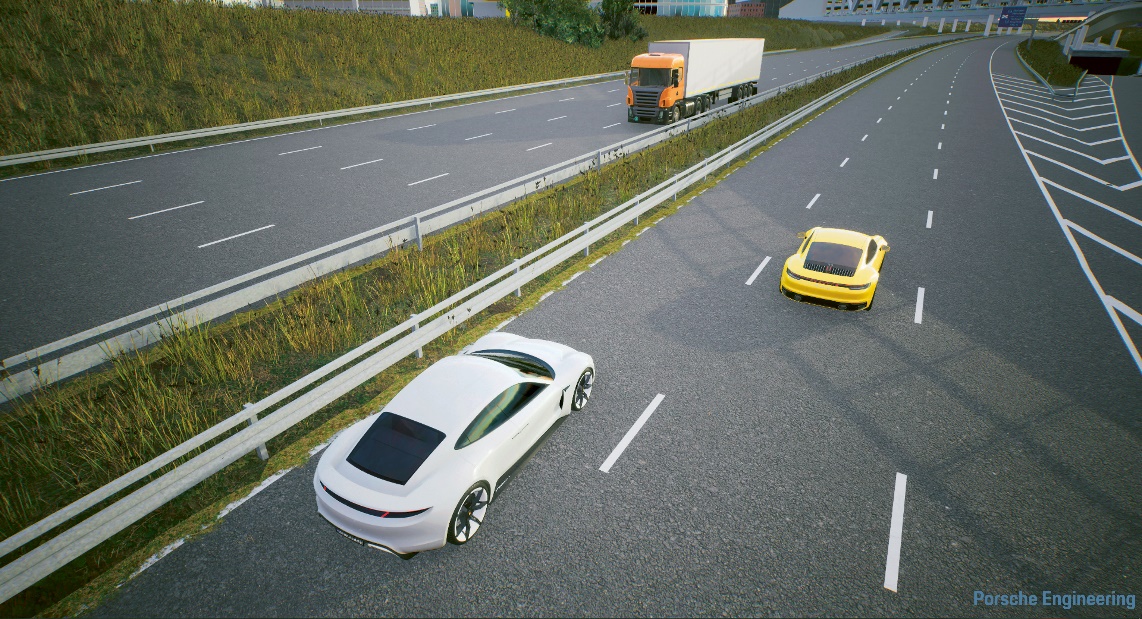
There are still a few hurdles to clear on the road to highly automated and autonomous driving. In critical driving situations, such as a tight overtaking maneuver by an oncoming vehicle, a child running into the road or a violation of the right of way, human drivers usually prevent an accident. How can we test automated vehicles and ensure that they will respond just as well in the future—or, optimally, even better?
A consortium from industry and research is investigating this issue within the AVEAS project, which is concerned with the determination, analysis, and simulation of critical driving situations, and is funded by the German Federal Ministry of Economics and Climate Protection (BMWK). Consortium members include Porsche Engineering, Continental, and the Allianz Center for Technology, as well as other partners such as KAMO partners PTV, Fraunhofer IOSB and KIT. In the project, scenarios are simulated using not only a real test vehicle but also its digital twin. This is because real test vehicles cannot cover the billions of test kilometers needed for a robust validation of the technology. Above all, it is also costly and risky to test hazardous situations such as emergency braking in front of a traffic jam, or abrupt changes of direction on wet leaves, snow or in poor visibility conditions in real road traffic. The real scenarios—significantly expanded—are therefore transferred to the digital twin in the simulation. »We are building a catalog of critical scenarios that will enable us to validate driver assistance systems and functions for highly automated driving,« explain Tille Karoline Rupp, who is responsible for simulation at Porsche Engineering, and Dr. Joachim Schaper, Head of AI and Big Data at Porsche Engineering. Two of the simulation tools used in the project result from combining expertise in Karlsruhe: KAMO, PTV Vissim and the Fraunhofer OCTANE project. More information about the AVEAS project can be found at: https://aveas.org/
How do research results reach the market? – example of an innovative battery module for e-vehicles
In addition to collaborative research between industrial and research partners within the framework of funded projects, the KAMO partners also cooperate directly with industry, working with customers to further develop ideas and successfully transfer them onto the market. Based on preliminary work and the know-how of the KAMO partners, pre-competitive research and development results can be adapted to specific customer requirements.
One example is the cooperation between Sumitomo Bakelite Europe (Ghent) NV (SBEG) and the Fraunhofer Institute for Chemical Technology ICT. The joint devel-opment was a battery module made out of SBEG composite materials, which has a lightweight construction resulting in high energy density, an innovative cooling concept that improves the longevity and rapid-charging capability of the batteries, a novel safety concept for a thermal runaway scenario, and integrated functions that save money and space. Secured by patents, this module is now being jointly mar-keted.
Contractual agreements drawn up prior to the collaboration determine whether the patents arising in bilateral projects are filed and used jointly, and thus exploited by all partners involved, or whether the industrial partner owns exclusive rights of use and exploitation.
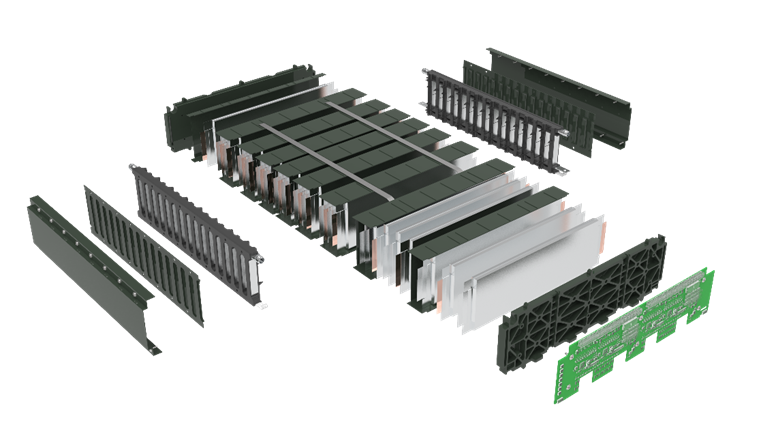
Use of the lower airspace for urban traffic
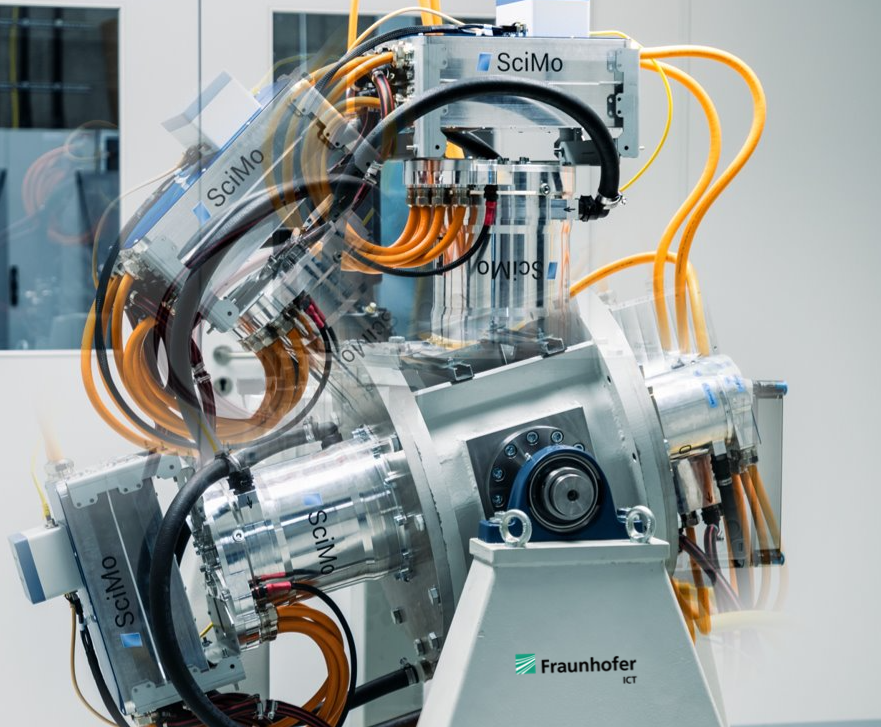
It is now a realistic scenario for the coming years that urban transport will use the lower airspace, to reduce the strain on ground infrastructure, seal less land, enable a higher quality of life in cities and still meet the growing need for passenger and freight mobility. Accordingly, the supply of aircraft and drones is currently growing rapidly to serve this market.
In order to test the propulsion systems for the first flight and to compare them with the pure simulation results, a hardware-in-the-loop-capable (HiL-capable) propulsion test rig for urban air mobility applications was designed and built by KAMO partner Fraunhofer ICT. This significantly shortens the development time of the propulsion systems, and thus significantly reduces the development costs. The swivel test rig enables controlled and reproducible test conditions to be generated in a simulated environment. In the context of the Fraunhofer ALBACOPTER® project, the simulation environment OCTANE of the KAMO partner Fraunhofer IOSB was combined with this rig. On the test rig, powertrain performance can be monitored, enabling data-driven decision making.
The following test cases have already been implemented:
Thermal tests for electric engine cooling systems (oil spray cooling, water jacket, rotor cooling, others), inverter and gearbox systems, endurance tests, overload tests, cooling and lubrication tests. Tilt ranges of +/- 90° at max. angular velocities of 165°s can be created.
»Propulsion systems with speeds of up to 6,000 rpm, max. torque of 500 Nm and max. power of 300 kW can be tested in a realistic environment,« says project manager Dr. Lars-Fredrik Berg, who is Deputy Director of the New Drive Systems Department at Fraunhofer ICT.
»The construction of the HiL-capable swivel test rig is a good example of how we can pool the expertise of our KAMO partners to create new options for businesses,« says KAMO office manager Dr. Miriam Ruf. In addition to the testing rigs, the partners also have the expertise needed to support the further development of electric motors and drive systems.
The KAMO: Karlsruhe Mobility High Performance Center
KAMO is the central contact point in Karlsruhe for innovative mobility solutions for interregional and international players from business, politics and civil society. The Karlsruhe Mobility High-Performance Center represents the interdisciplinary development and support of forward-looking mobility and logistics solutions, covering entire systems.
Through the well-established cooperation by the Karlsruhe partners in research, development and teaching in mobility and logistics, all levels of innovation are covered. Together with our customers and partners from business, science and civil society, innovations are brought quickly and reliably into application.
KAMO’s research partners are: Fraunhofer (with the institutes ICT, IOSB and ISI), the Karlsruhe Institute of Technology KIT, the FZI Research Center for Information Technology and the Karlsruhe University of Applied Sciences HKA.
Stay In Touch